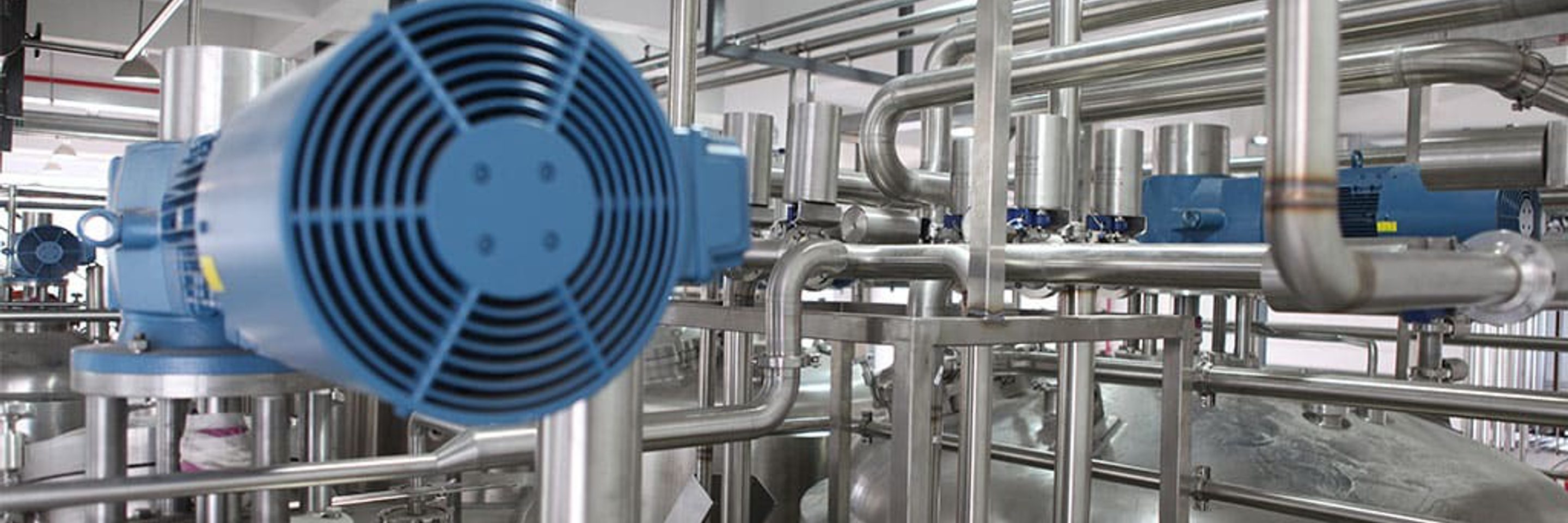
While COVID has wreaked havoc on global health systems, its impacts on supply chains have been just as pronounced. But rapid advancements in manufacturing technology could provide a possible answer for a global shipping industry teetering near the brink of collapse.
If the first two weeks of 2022 are anything to go by, it’s looking increasingly likely the disruptions and delays that plagued supply chains over the course of the pandemic will continue to escalate.
An emerging technology, however, could be shaping up as a panacea for manufacturers and global shipping companies as they navigate a perfect storm of congested ports, sky-high container costs and shortages of key manufacturing components and construction materials.
Since the onset of COVID-19, global shipping networks have been under immense strain, with workforces decimated by the virus forcing lockdowns and large-scale factory shutdowns.
Throughout 2021, the coronavirus-related pressures were exacerbated as several unexpected and unpredictable events added more burdens on an industry facing unprecedented pain.
In the United States, the country’s petrochemical supply chain was all but shut down by February’s big Texas freeze, with production of plastics, resins and other key manufacturing components slowing to a halt.
Then came Hurricane Ida, which halted freight movement across the Gulf Coast, while inland container terminals from California to Chicago became clogged and congested as logistics operations battled to keep pace with a surge of import volumes. The Ever Given blocked the Suez Canal and catastrophic flooding hit European supply chains.
Collectively, virus-related disruptions, unexpected events and natural disasters resulted in massive economic hardship, with a 2021 survey of 900 international shipping companies by Statista showing an uptick of average annual costs of $US184 million.
While the cost of goods and growing delays are the obvious symptoms of the supply chain chaos, it can also mean ordinary businesses grinding to a halt.
Across the world, companies report waiting months for single replacement parts that are needed to get machines moving or products completed.
A fledgling fix
But there could be hope on the horizon, with rapid advancements in additive manufacturing technology having the potential to emerge as a solution to some of the world’s supply chain woes.
Colloquially referred to as 3D printing, which in some circles has been dismissed as a gimmick, additive manufacturing is a diverse set of technologies that create three dimensional objects through the layering of materials in precise shapes using computer-aided-designs or 3D scanners.
It’s seen as a potential solution by major manufacturing giants such as Siemens, which is testing additive manufacturing as a way of “printing back” the damaged area of gas turbine blades, rather than replacing them, as an example of how the process can be used.
“In remote construction or industrial sites, shipping replacement parts in can be an expensive and time-consuming process because for many of these activities, downtime has a direct line to lost profits,” the company said in an article released last year on the Siemens blog.
“Field repair would no longer mean limping the machinery along until the replacement comes in, it would mean bringing the machine back up to complete operation in a few hours if there is a printer onsite.”
Chris Barlow, a manufacturing partner at UK-based MHA, an independent member of Baker Tilly International, said there were some significant advantages to additive manufacturing that could help solve some of the shipping industry’s most pressing problems.
“One of the biggest challenges we are seeing in supply chains at the moment is the inability to get the right product in the right place,” Mr Barlow said.
“We’ve seen container costs go up, we’ve seen issues around the UK in terms of getting products into the UK because of customs issues, we’ve seen shortages of particular products, we had floods in Germany, we’ve had production issues in China, and that’s not even mentioning the global pandemic.
“The benefit of additive manufacturing is you have the design, and you sit there, and you print it.
“That sounds slightly flippant, but fundamentally, that’s what it is.
“It can reduce the steps in the supply chain by having the machine on site where you need it, with total control over it.
“By having the additive manufacturing machine exactly where you want it, you’re also not beholden to your supplier in terms of them buying, tooling or making changes to the machine.
“You can do exactly what you want, when you want and that’s its biggest advantage.
“There is also the green angle; additive manufacturing cuts emissions, cuts waste and cuts the use of harmful materials by taking them out of the production chain
“It’s a solution for supply chains and it does slash emissions, those are its biggest advantages.”
Data security and training
Mr Barlow said additive manufacturing allowed for the creation of digital inventory libraries, which when combined with an additive manufacturing machine reduce the need to ship parts or components from warehouse to warehouse.
But while it sounds convenient, he said a digital inventory created new challenges for manufacturers and logistics firms.
“The issue that we have got to be aware of when we are talking about the technology aspect is data security,” Mr Barlow said.
“Cybercrime is an issue across the world, and the more we utilise such machinery, cybercrime will become a more significant issue and could halt production for a period of time.”
“We are talking about something that is very much open to issues of cybercrime, and that’s got to be a consideration that businesses take seriously as part of that.
“Cybercrime is an issue across the world, and the more we utilise such machinery, cybercrime will become a more significant issue and could halt production for a period of time.
“Whereas, a traditional lathe sitting in a manufacturing workshop, you have physical security over it, which is not the same with these sorts of machines that we’re talking about.”
Other challenges that need to be addressed before additive manufacturing was widely adopted as a solution are several limitations with the technology, as well as the significant costs involved in installing a printing machine and training employees to operate it.
To solve the training issue, Mr Barlow said industry would look to governments to provide incentives to upskill their workforces, but for the other challenges, there needed to be a change in mindset regarding the best use of additive manufacturing technology.
“In my knowledge and experience, the printing machines are not as quick as a traditional manufacturing machine, so one of the issues that we would need to overcome for wide scale adoption is to be able to speed up that process,” Mr Barlow said.
“At the moment, because of the barriers to entry in low level areas in terms of manufacturing high volumes of production parts at a small cost, such as screws, nuts, bolts, etcetera, that’s not where it’s at because of the limits involved.
“What I’ve seen it used for are boats, excavators, jet engine turbines, or robotic hands, for example.
“It’s at the higher level, to be able to produce something that’s complicated and very niche, that’s where the advantage sits at the moment.
“They are great for printing something that is particularly niche or particularly wanted at a particular stage, but those machines are not yet at the stage of being able to mass produce something, and that’s a hurdle that we need to overcome.
“At the moment, it’s something that can be used alongside traditional manufacturing.”
Mr Barlow said he expected momentum to build considerably in the additive manufacturing space as manufacturers sought lower emissions solutions, but a trailblazer would be necessary to launch the technology into the mainstream.
“It’s great to say, ‘we printed a robotic hand’ but actually we need somebody to say, ‘I printed several parts of this everyday product’,” he said.
“It needs to be something that everyone uses to be championed rather than something at the high end.
“The risk is, because we can go on about the big things and the impressive things that have been produced, potentially manufacturers will switch off and say, ‘that’s great, but I don’t do that’.
“It’s about making sure that we don’t glamourise it too much, there is a balance to be had.
“It is fairly versatile; it’s not going to create mass produced parts and there needs to be a balance between that.
“People don’t need to be wowed, they need to bring the focus down a little bit and explore the potential to develop the products they need.”
A demonstration of that everyday potential is emerging in Canada, according to Baker Tilly Windsor LLP consultant Kassem Nizam.
Mr Nizam said additive manufacturing was starting to take off in Canada, with many manufacturers adopting the approach of having a 3D printer in-house, which has not only reduced lead times in obtaining items but also provided a boost to research and development and product prototyping.
Mr Nizam said additive manufacturing was starting to take off in Canada, with many manufacturers adopting the approach of having a 3D printer in-house, which has not only reduced lead times in obtaining items but also provided a boost to research and development and product prototyping.
“The pandemic has shed the light on how dependent we are on other countries for our manufacturing need,” he said.
“And it could all just stop right now, without any ships being able to come into Canada, we can’t get our products.
“It’s made us look in our own backyards a little bit more into how to manufacture our own things.
“That has shed some light on 3D printing. I remember when this pandemic first started, I had some friends at the University of Michigan who had started 3D printing face shields, because there was a shortage of face masks.
“So that was an area where 3D printing really became very valuable to us.”
Mr Nizam said as technology continued to develop, he expected additive manufacturing to play a more prominent role across industries.
“What we’ve seen in the past couple years with the more advanced technology gets, the faster we advance in the future.
“So, with this whole new era of advanced electronics and being more environmentally friendly, I think additive manufacturing really ties in with all of that.”